The Cognito EODD Pump Journey in Detergent Manufacturing
Market/Application Overview
In detergent manufacturing, transferring highly concentrated slurries requires reliable and efficient pumping solutions. As manufacturers seek operational efficiency and cost-effectiveness, selecting the right pump technology is crucial for optimizing production processes for such highly abrasive and corrosive mediums.
The Need for a Reliable Pump
A leading detergent manufacturer from UAE faced significant challenges with their existing Progressive Cavity (PC) pumps. Frequent breakdowns and severe leakage issues resulted in high maintenance costs and substantial downtime, severely impacting production capacity. Key performance indicators such as MTTR and MTBF were consistently high, hampering their operational efficiency and profitability.
Customer Challenges with Screw Pumps
High Maintenance Costs:
Due to frequent failure of sealing, stator, and rotor.
Inconsistent Performance:
Affecting production schedules.
Increased Downtime:
Leading to lost revenue opportunities.
Inventory:
Needs to maintain to continue production.
Process Details
The Right Solution:
Cognito EODD Pump
Recognizing the urgent need for a robust solution, the Cognito team engaged with the customer to understand their specific challenges and operational goals. After a thorough assessment, they proposed the 4" Cognito EODD pump.
The Cognito™ EODD pump excels in such challenging slurry applications due to its,
- Seal-less design: Cognito’s seal-less pump minimizes wear and tear through customized speed selection for abrasive media. In contrast, the seal design in the PC pump resulted in increased wear and tear.
- Robust diaphragm design: The stators and rotors of PC pumps are engineered to fit together with interference. However, in abrasive media, this tight fit causes considerable wear and tear at the contact points, leading to a shorter lifespan for both components in such demanding conditions. In contrast, the unique design of Cognito EODD pumps, specially designed for challenging media, prevents wear and tear, significantly extending lifespan.
- Safety feature: Advanced leak detection mechanism in Cognito™ EODD pump promptly identifies issues, reducing inspection frequency and enhancing operational safety.
- Innovative Stopper Cage Design: Protects critical components from abrasion, extending the lifespan of the manifold and check valves by 2 to 3 times, ensuring trouble-free operation.
This innovative pump was installed in the customer’s facility, with continuous support from the Cognito™ team to ensure it met all operational requirements.
The introduction of the Cognito™ EODD pump proved to be a game-changer. It effectively resolved the frequent maintenance issues and significantly boosted operational efficiency.
Customer Experience
The results following the implementation of the Cognito™ EODD pump were remarkable:
- Significant reduction in maintenance expenses.
- Quick spare replacement minimizing downtime and ensuring continuous operation.
- Minimal inventory management, cost savings and streamlined operations.
- Significantly reduced breakdowns, enhancing overall reliability.
- Improved performance and efficiency, leading to smoother operations.
- Quick return on investment (ROI) within just 1.5 years.
- Extended pump lifespan, contributing to long-term operational stability.
The deployment of the Cognito EODD pump not only resolved the detergent manufacturer’s immediate challenges but also set the stage for future growth.
By opting for this reliable and efficient solution, they significantly enhanced production capabilities and reduced operational costs. This case study illustrates how innovative pump technology can transform manufacturing processes, driving sustainability and profitability in a competitive market.
Download the Case Study
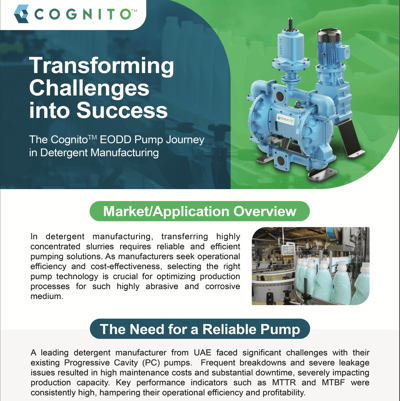
Want Your Organization To See Similar Results?
Contact an expert to learn more about our EODD pumps and how they can benefit your pumping operation.