Abrasive Slurry Transfer in Ceramic Insulators Industry
The Need
Ceramic insulators are typically made by shaping and firing a mixture of ceramic materials such as clay, silica, and alumina at high temperatures. Efficient slip transfer systems play an important role by significantly speeding up the production process, reducing downtime, and increasing overall productivity.
A top industry leader in the ceramic insulator sector was using a Progressive Cavity Pump for their abrasive slurry transfer application. However, they faced several challenges.
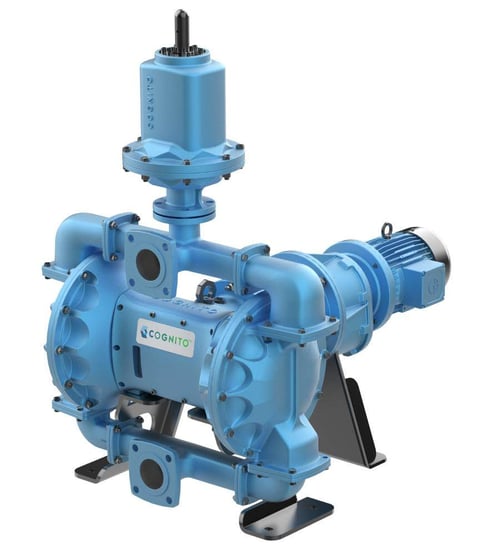
Customer Challenges
They were looking for a reliable pumping solution that could transfer abrasive slip efficiently and without any breakdown.
Elevated Maintenance Costs:
Frequent rotor and stator failures due to the abrasive nature of the operating liquid, resulting in significant maintenance costs.
Frequent Downtime:
The packing gland failures caused leakage issues, resulting in operational downtime.
Reliability Issues:
The existing Progressive Cavity Pumps were not reliable, affecting overall productivity.
Process Details
The Right Solution
The Cognito EODD pumps are specifically designed to handle highly abrasive fluids smoothly, thanks to its robust mechanism, patented diaphragm design, and the unique "Stopper Cage Design." In contrast, PC pumps often face wear and tear issues due to their interference fit of main mechanical rotary pumping technology, which are sensitive to abrasives and also not suitable to handle negative suction applications.
Our Cognito team presented how the robust design of Cognito EODD pump and its features can minimize breakdowns and lower the maintenance costs compared to PC pumps with quick return on investment. They also offered IoT-enabled remote monitoring feature for real-time performance tracking to provide customers with greater control of operation and to track the maintenance schedule, something that PC pumps could not offer.
The Cognito EODD pump has effectively replaced the 4” PC pump with our 3” EODD pumps, demonstrating the mentioned advantages and noticeable maintenance cost savings.
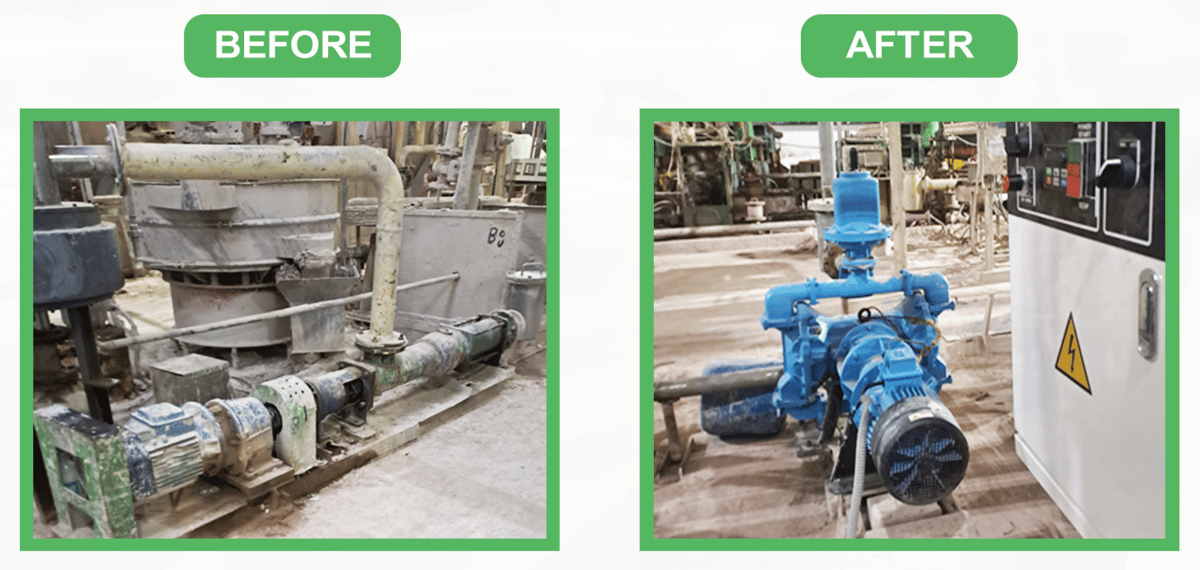
Customer Experience
Switching to Cognito’s EODD pumps has been transformative for the customer. They reported substantial reductions in energy costs, maintenance expenses, and downtime. They are very happy with the pump performance and efficiency, having replaced their 15 nos. of 4” PC pumps with our 3” Cognito EODD pumps in a year.
Post-implementation, the customer observed significant improvements:
Significant reduction in maintenance cost
Reduce energy costs by 50%
Achieved ROI in less than a year
Improved total cost of ownership
Energy Consumption Comparison: PC Pumps vs. Cognito EODD Pump
Maintenance Comparison: PC Pumps vs. Cognito EODD Pump
The customer conveyed their immense satisfaction with the Cognito pumps.
They highlighted that the switch from PC pumps to EODD pumps has greatly enhanced their operational efficiency and overall cost savings.
Download the Case Study
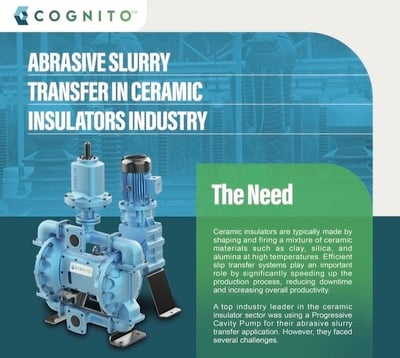
Want Your Organization To See Similar Results?
Contact an expert to learn more about our EODD pumps and how they can benefit your pumping operation.